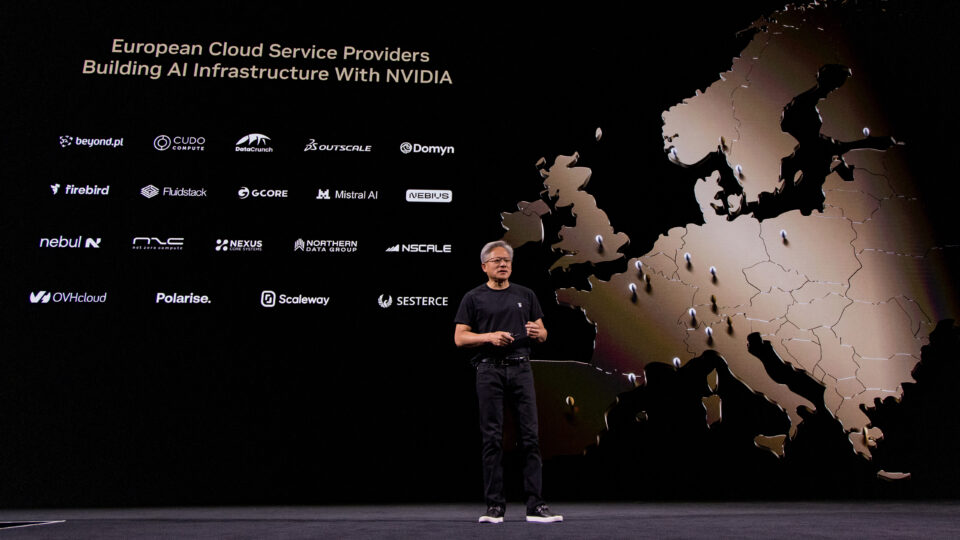
At GTC Paris — held alongside VivaTech, Europe’s largest tech event — NVIDIA founder and CEO Jensen Huang… Read Article
At GTC Paris — held alongside VivaTech, Europe’s largest tech event — NVIDIA founder and CEO Jensen Huang… Read Article
AI supercomputing is accelerating the development of new quantum applications, driving breakthroughs in critical industries such as aerospace, automotive and manufacturing. Underscoring that opportunity, Ansys announced today it is using… Read Article
Sovereign AI has sparked a new Italian renaissance around industrial transformation. Supporting its design and manufacturing heritage, Italy is among leading European nations in its advanced development of sovereign AI…. Read Article
Germany’s Leibniz Supercomputing Centre, LRZ, is gaining a new supercomputer that delivers roughly 30x more computing power compared with SuperMUC-NG, the current LRZ high-performance computer. It’s called Blue Lion. And… Read Article
U.K. Prime Minister Keir Starmer’s ambition for Britain to be an “AI maker, not an AI taker,” is becoming a reality at London Tech Week. With NVIDIA’s support, the U.K…. Read Article
Ready for a front-row seat to the next scientific revolution? That’s the idea behind Doudna — a groundbreaking supercomputer announced today at Lawrence Berkeley National Laboratory in Berkeley, California. The… Read Article
Over a century ago, Henry Ford pioneered the mass production of cars and engines to provide transportation at an affordable price. Today, the technology industry manufactures the engines for a… Read Article
Researchers across Taiwan are tackling complex challenges in AI development, climate science and quantum computing. Their work will soon be boosted by a new supercomputer at Taiwan’s National Center for… Read Article
Oracle has stood up and optimized its first wave of liquid-cooled NVIDIA GB200 NVL72 racks in its data centers. Thousands of NVIDIA Blackwell GPUs are now being deployed and ready… Read Article