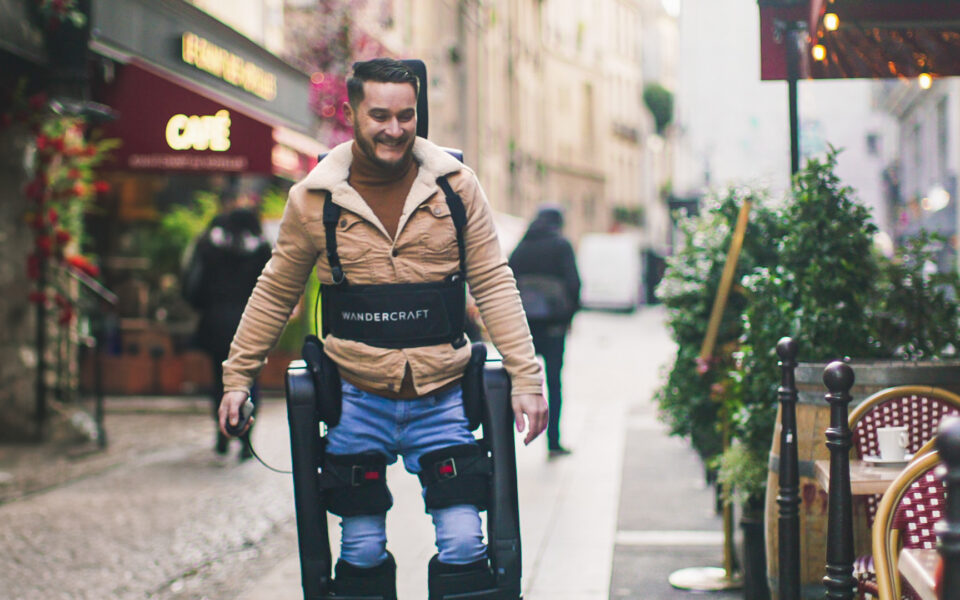
For Nicolas Simon, advancing the field of robotics is a personal mission that could change his siblings’ lives…. Read Article
For Nicolas Simon, advancing the field of robotics is a personal mission that could change his siblings’ lives…. Read Article
This National Robotics Week, NVIDIA highlighted the pioneering technologies that are shaping the future of intelligent machines and driving progress across manufacturing, healthcare, logistics and more. Advancements in robotics simulation… Read Article
Advances in physical AI are enabling organizations to embrace embodied AI across their operations, bringing unprecedented intelligence, automation and productivity to the world’s factories, warehouses and industrial facilities. Humanoid robots… Read Article
Teaching autonomous robots and vehicles how to interact with the physical world requires vast amounts of high-quality data. To give researchers and developers a head start, NVIDIA is releasing a… Read Article
Every second, businesses worldwide are making critical decisions. A logistics company decides which trucks to send where. A retailer figures out how to stock its shelves. An airline scrambles to… Read Article
The NVIDIA Isaac GR00T Blueprint for synthetic motion data significantly accelerates the data generation and training of humanoid robots…. Read Article
The next frontier of AI is physical AI. Physical AI models can understand instructions and perceive, interact and perform complex actions in the real world to power autonomous machines like… Read Article
According to Gartner, the worldwide end-user spending on all IT products for 2024 was $5 trillion. This industry is built on a computing fabric of electrons, is fully software-defined, accelerated… Read Article
Generative AI and foundation models let autonomous machines generalize beyond the operational design domains on which they’ve been trained. Using new AI techniques such as tokenization and large language and… Read Article