The ultimate in AI technology is now helping build the ultimate driving machine.
As part of NVIDIA’s GTC 2020 conference, BMW Group announced it is redefining factory logistics with NVIDIA’s Isaac robotics platform, enhancing its factory logistics processes with advanced AI computing and visualization for logistics robots based on the NVIDIA Isaac SDK and Isaac Sim simulation platform.
In the early 1900s, when Henry Ford began production of the Ford Model T, the vehicle was sold with essentially no options. Ford was famously quoted at the time as saying, “You can have any color as long as it’s black.”
More than a century later, BMW Group offers 40 different models, each with an average of 100 different options. If each option has at least two choices, then the factory logistics team is dealing with 2100 possible configurations they need to organize parts for — so many it would take hundreds of thousands of years to list them all out loud.
Simultaneously, demand has significantly increased, doubling over the last 10 years to 2.5 million cars a year. BMW Group customers submit close to 10,000 new car orders a day. More than 99 percent of those vehicle orders are different from each other.
In other words, almost every order is custom. This means the BMW Group Factory Logistics team must take in 30 million raw parts a day, from 1,800 suppliers, at 31 different factories around the world, and organize them into custom parts trays — for every customer order.
Assembly is happening on a line that could have up to 10 different models going through at the same time. One vehicle could be an SUV, the next a sedan, the third, a sports car. The right parts to build each needs to be organized and delivered to the correct car, just in time, just in sequence. The line outputs a new car every 56 seconds, and the line can never stop.
Bring in the Robots
Achieving this miracle of factory logistics requires a level of accuracy and synchronization beyond what has existed previously.
Intelligent production begins with AI-powered logistics robots. BMW Group is developing five new types of robots on the NVIDIA Isaac robotics platform, powered by NVIDIA Jetson and EGX edge computers and running on a single NVIDIA Isaac SDK software architecture. These robots are trained and validated on Isaac Sim.
Three of these robots — the SplitBot, PickBot and PlaceBot — are responsible for placing boxes of raw parts on the line and transporting them to shelves to await production.
The Smart Transport Robot is an autonomous delivery navigation robot, which picks up these trays of parts and moves them to an area to be taken by a “tugger train” to manufacturing. STR is powered by NVIDIA Jetson AGX Xavier, which delivers up to 32 trillion operations per second of performance for perception, pose estimation, 3D human pose estimation, localization, path planning and actuation.
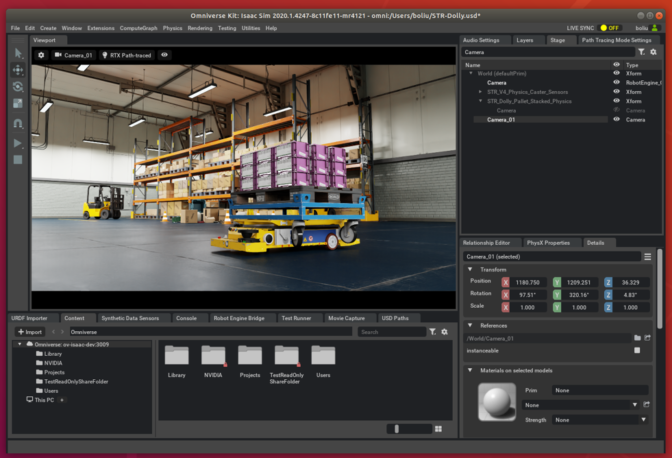
Finally, the SortBot manipulation arm, which also runs on Jetson AGX Xavier, takes the empty boxes and puts them on a palette to be sent back to the supplier area.
One Scalable Architecture
This entire family of logistics robots was developed using a single software architecture, running on the open NVIDIA Isaac robotics platform. The Isaac SDK provides a comprehensive set of tools, libraries, reference robot applications, pre-trained DNN algorithms and TAO Toolkit to adapt the deep neural networks to different robots.
The robots are then tested and validated using Isaac Sim for navigation and manipulation. This virtual proving ground significantly streamlines communication as well as widens the environments in which the robots are tested to a near-infinite range of scenarios.
The NVIDIA Isaac robotics platform allows BMW Group to easily manage new models, brands and configurations to anticipate and meet customer demand, using leading AI technology to innovate factory logistics for the century to come.