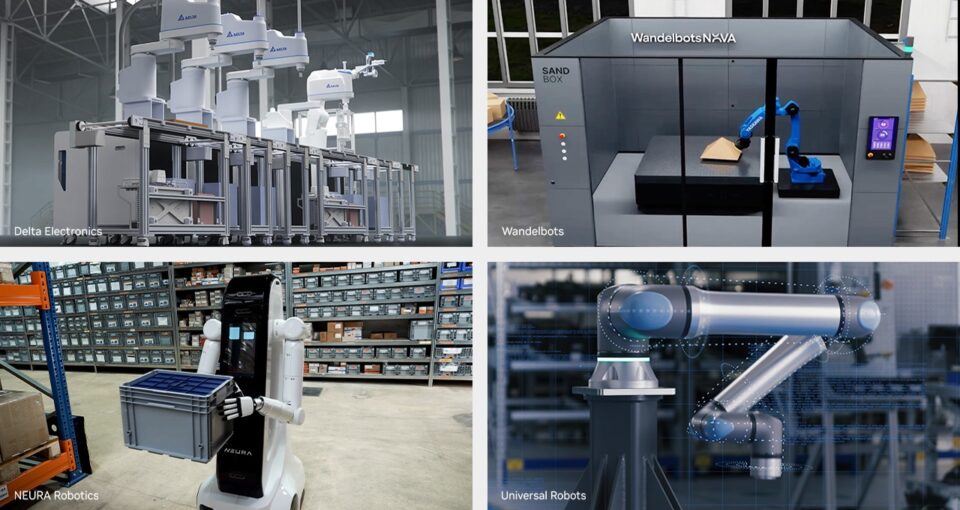
NVIDIA and Partners Highlight Next-Generation Robotics, Automation and AI Technologies at Automatica
From the heart of Germany’s automotive sector to manufacturing hubs across France and Italy, Europe is embracing industrial… Read Article
From the heart of Germany’s automotive sector to manufacturing hubs across France and Italy, Europe is embracing industrial… Read Article
NVIDIA Research is advancing methods that combine robotic simulation, optimization and AI to enable more generalizable and adaptable robot behavior. At this year’s Robotics: Science and Systems (RSS) conference, taking… Read Article
As a global labor shortage leaves 50 million positions unfilled across industries like manufacturing and logistics, Hexagon — a global leader in measurement technologies — is developing humanoid robots that… Read Article
In the face of growing labor shortages and need for sustainability, European manufacturers are racing to reinvent their processes to become software-defined and AI-driven. To achieve this, robot developers and… Read Article
Germany is building on a long history of engineering innovation with new AI investments poised to transform the country’s economy — including the automotive, banking, manufacturing and robotics industries. The… Read Article
Since a 7.8-magnitude earthquake hit Syria and Türkiye two years ago — leaving 55,000 people dead, 130,000 injured and millions displaced from their homes — students, researchers and developers have… Read Article
Across robot training and development, NVIDIA Research is uncovering breakthroughs in areas such as multimodal generative AI and synthetic data generation. The team’s latest innovations will be spotlighted at the… Read Article
The world’s largest electronics manufacturer is building smart hospital solutions using NVIDIA technologies from the data center to the edge…. Read Article
Leading healthcare organizations across the globe are using agentic AI, robotics and digital twins of medical environments to enhance surgical precision, boost workflow efficiency, improve medical diagnoses and more. Physical… Read Article