Silicon Valley magic met Wednesday with 175 years of industrial technology leadership as Siemens CEO Roland Busch and NVIDIA Founder and CEO Jensen Huang shared their vision for an “industrial metaverse” at the launch of the Siemens Xcelerator business platform in Munich.
“When we combine the real and digital worlds we can achieve new levels of flexibility and we can bring new products to market faster,” Busch said during an event at Siemens’ Munich headquarters.
Pairing physics-based digital models from Siemens with real-time AI from NVIDIA, the companies announced they will connect the Siemens Xcelerator and NVIDIA Omniverse platforms.
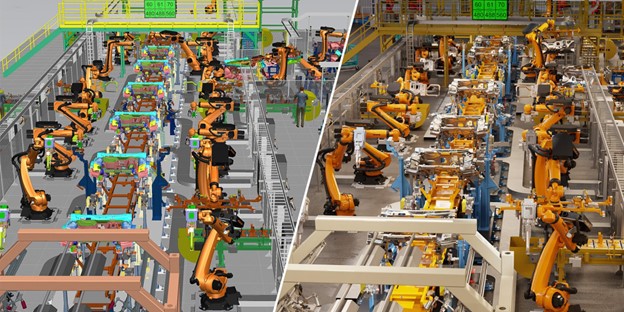
“With our two companies we can connect what Siemens makes with what NVIDIA makes, to AI and Omniverse,” Huang said. “We can now fuse data from the point of design, all the way through product life cycle management, all the way through the automation of plants to the optimization of the plant after deployment — that entire life cycle can now be in one world.”
Bringing Real, Virtual Worlds Together
Siemens Xcelerator is a business platform that includes internet of things-enabled hardware, software and digital services from across Siemens that offer a comprehensive digital twin that can bring together the mechanical, electrical and software domains.
Siemens is a leader in industrial automation and software, infrastructure, building technology and transportation, and their solutions are used across the manufacturing lifecycle from designing products and the equipment to manufacture those products in factories to controlling and tracking how the equipment moves to orchestrating the flow of people, parts and machines across the factory itself.
The company has built a rich portfolio of hardware and software solutions that are part of the Siemens Xcelerator platform that is now at the center of an ecosystem of more than 50 certified partners
The NVIDIA Omniverse 3D collaboration and simulation development platform delivers photorealistic rendering capabilities and advanced AI to the Siemens Xcelerator ecosystem, allowing the digital twin to be represented in full-design fidelity, and operating in real time.
Working Side by Side
During Wednesday’s event, Busch and Huang outlined their plans, showed a demo video of these technologies working together, and sat down for an informal fireside chat with Milan Nedeljkovic, a member of the board of management of BMW.
“The digital twin itself is not the challenge,” Nedeljkovic said, outlining BMW’s plans to create sophisticated digital models of its manufacturing process that are linked, in real time to real-world factories. “The challenge is to link into this digital twin the existing systems one by one, and to have any change in the digital twin being reverted in the original planning tools.”
Busch and Huang began their conversation by sharing the story behind Wednesday’s news, relaying insights from their meeting in November.
“We figured out that when we bring our competencies, our technology, our platforms together, we can do something great,” Busch said. “We can basically go for the full-fledged industrial metaverse … to have faster decisions, real-time decisions with higher confidence.”
Transforming Businesses
With the connection of Siemens Xcelerator and NVIDIA Omniverse, manufacturing customers of any size will be able to immediately analyze issues, identify root causes, and simulate and optimize solutions, thanks to the AI-infused, real-time photorealistic virtual environments, Busch and Huang said.
So, for example, if something goes wrong on the factory floor, teams of users from around the world will be able to meet, virtually, to collaborate and use the connected digital twin to quickly identify, troubleshoot and solve the problem.
The partnership also promises to make factories more efficient and sustainable. Users will more easily be able to turn data streaming from the factory floor PLCs and sensors into AI models. These models can be used to continuously optimize performance, predict problems, reduce energy consumption, and streamline the flow of parts and materials across the factory floor.
Under the Hood
The partnership brings together complementary technologies and ecosystems, the two leaders said.
Innovating at the intersection of real and digital worlds, Siemens offers the industry’s most comprehensive digital twin by representing the mechanical, electrical and software domains interacting, Busch explained.
NVIDIA Omniverse is a multi-GPU scalable virtual world engine that enables teams to connect 3D design and CAD applications for collaborative design workflows and allows users to build physically accurate virtual worlds for training, testing and operating AI agents such as robots and autonomous machines.
Together, Xcelerator and Omniverse offer a powerful combination of capabilities.
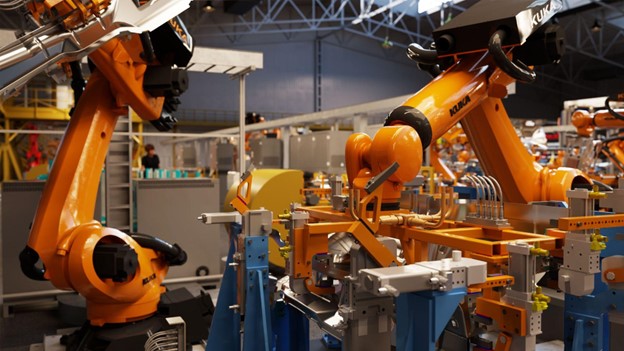
For example, energy and utility plant engineers can virtually navigate through the live digital twin of a facility to analyze the thermal distribution produced by the existing air conditioning. system from Siemens simulations.
Then they can explore different vents and cooling towers configurations, powered by use the of Omniverse’s full-design-fidelity visualization capabilities enabled by real-time ray- and path-traced rendering.
Ultimately every component inside a factory can be inspected and optimized — and eventually, automated by AI. A robotic conveyer belt could be trained to alert an operator when the conveyor motor is undergoing excessive energy draw due to improperly greased rollers, saving time and maintenance costs, for example.
Advancing Digital Twins
These innovations will reach not just from the cloud to the factory floor, but across industries, Busch and Huang explained.
“You know, if you look at almost every engineering project today of any significant complexity, we simulate the product before we go to production,” Huang said. “And yet, for most plants and most factories, it’s nearly impossible to do that today … and so we needed to create a very large-scale simulation platform: Omniverse.”
The addition of Siemens Xcelerator to the Omniverse ecosystem will enable domain-specific digital twins, using the rich design, manufacturing and operational data from Siemens’ mechanical, electrical, software, IoT and edge solutions in Omniverse.
“The world’s industries represent hundreds of trillions of dollars over time,” Huang said, adding that finding even small efficiencies in such huge systems is a huge opportunity. “That’s one of the reasons why people want to invest and now we have the technology capability for them to do so.”
BMW’s iFACTORY
The two CEOs continued the fireside chat with BMW AG’s Member of the Board of Management, Milan Nedeljković.
Nedeljković outlined the carmaker’s initiative, dubbed iFACTORY, to make its factories “lean, green and digital.”
And he explained how BMW Group is working with both Siemens and NVIDIA to move this effort forward.
“By the end of next year BMW will offer 13 fully electrified cars,” he said. “So we are changing our equipment, we are changing our production environment, we are changing our processes, and all of that needs good planning, and, again, digitization is a part of it.”
Siemens and NVIDIA are continuing to help BMW with this digital transformation with the companies committing to collaborate to develop BMW’s factory in Debrecen, Hungary.
BMW is moving fast, planning to get the factory running by 2025. That means Siemens and NVIDIA, who will help BMW model the factory, will need to move fast, too.
“We’re going to make it happen,” Huang said.
Learn more about Siemens and NVIDIA’s partnership.